Make a Splash with Color: A Move to Inkjet Fits the Bill for KUBRA
November 19, 2020
The following article was published in Paper Matters – Fall Digital Edition Vol. XIV.
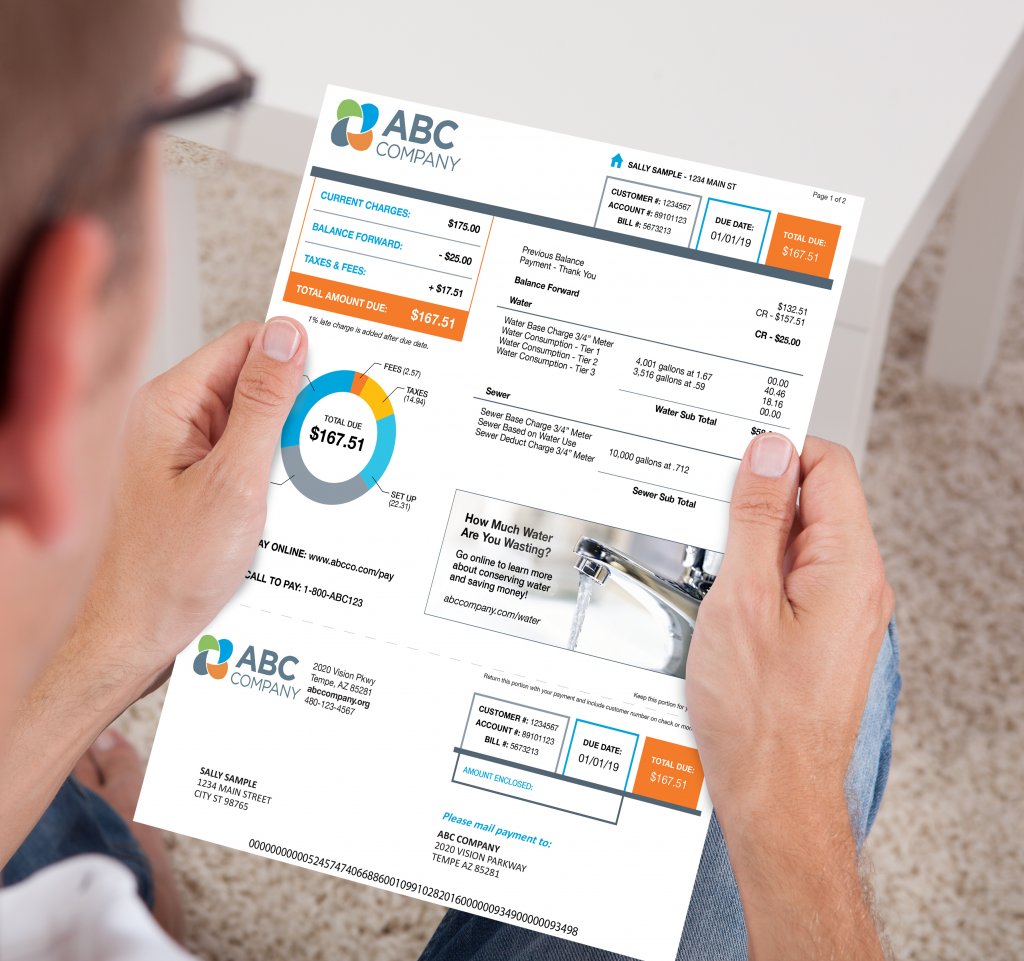
So many consumers get their bills via email, we often forget that a large portion of people still opt for paper bills.
And they have good reason. Many people prefer tangible documents because they’re easier to track, stack, organize and pay. And some customers—particularly those in rural locations—have no access to reliable internet, so choosing paperless billing isn’t even an option.
KUBRA, headquartered in Canada, with locations in Arizona, Texas, California and New Jersey, is a billing and payments company that offers both paper and electronic options. KUBRA’s goal is to provide super-fast, flexible service to their clients—and one way they’ve accomplished this is by switching from toner-based printing to inkjet.
Clients Lead the Way
The push to change came from one of KUBRA’s larger clients, a major utilities company in Canada. They wanted to use color for their paper billing because studies have shown that using colors on a paper bill can improve the customer experience and even speed payments. KUBRA was eager to take this on, and it required the company to move from toner-based to inkjet printing. According to Rob Iantorno, VP of Operations at KUBRA, the biggest challenge to making this switch was just trying to understand how everything worked. “We were going from a preprinted form that already had a perf on it to a blank page we had to add perfing to,” he says. “Also, before we were printing on 8 1/2″ x 11″ shells. Now we were running two-ups and slicing them down the middle to create the two pages.”
The Inkjet Advantage
Once KUBRA started to replace their monochrome toner-based printers with Canon G3900 inkjet printers, Iantorno discovered that inkjet offers significant advantages over thermal. Most surprising was the ease of use. “We thought we were getting into something complicated at the time,” he recalls. “But now we want to push more clients to color because it’s so simple.” The new system is also more dependable. Inkjet machines don’t go down as much since there’s no heat involved; with thermal printing, too much heat can result in premature print head failure.
Inkjet equipment is faster than thermal printers, according to Iantorno, and is more flexible as well. KUBRA can include more information on the page, dynamically change details and offer onserts—like bill inserts except printed in-line on the bill itself.
Perhaps the most attractive feature was that inkjet is a lot cheaper than toner. KUBRA had found toner-based printers to be very expensive to operate since they broke down so often. Inks and cartridges were a lot more expensive too; inkjet ink is just a third of the cost of toner.
KUBRA passes off the savings and flexibility to the client. Says Iantorno, “We tell clients, ‘We can redesign your bill, we can do it in color, we can be extremely flexible with changes, and we can do this in most cases for less than your current. Service levels will increase, no chance of stock issues, and changes can be made quickly.'”
The Paper Chase
A key to adapting to the new inkjet system was finding the right paper. “Paper plays a huge role,” says Iantorno. “Colors change depending on the paper we use. We also wanted to limit our clients—we didn’t want to start offering five different types of white paper. So we played around with a lot of papers and there were two that we chose as our primary.” When KUBRA looked for paper, they considered the brightness, how the colors laid on the paper and how the colors changed—a crucial consideration when printing clients’ logos, which needed to be the exact right color every time. KUBRA also wanted something that could handle the inks and the perforation. Finally, as they changed from preprinted forms to inkjet-printed forms, they wanted the look and feel to be the same. Domtar “fit the bill” for KUBRA. “We had a whole lineup of paper samples in order to decide which papers we were going to go with,” Iantorno said. “We went with 24 lb., and when I pick it up I almost have trouble telling between the inkjet and the offset.” The issue of availability helped seal the deal. “Nobody has paper anymore,” says Iantorno. “All these mills are moving to make cardboard. Availability, service, support—that’s where Domtar has been there for us.”
A Bright Future
Iantorno sees more and more pieces coming in the mail that are clearly inkjet printed, and says that quality in inkjet delivery has improved 100 percent over the years. Quality only continues to get better as the inks, colors and printer heads are improved. As inkjet equipment advances and KUBRA’s facilities become more efficient, the company can do more with less, replacing two machines with one that does twice the amount of work. The bottom line for KUBRA is keeping their clients happy. “We’re always looking at new technology, something that gives us that edge,” says Iantorno. “Clients want same day, not next day. We look for equipment that gives us that speed advantage, along with the quality and integrity our clients expect.” So far, the switch to inkjet for paper billing is paying off for KUBRA.
The original article can be found at https://viewer.ipaper.io/domtar/domtar-paper/paper-matters-magazine/153908papermattersdigital-fall-2020ssingles/?page=14